Jak ocenić stopień automatyzacji procesu produkcyjnego?
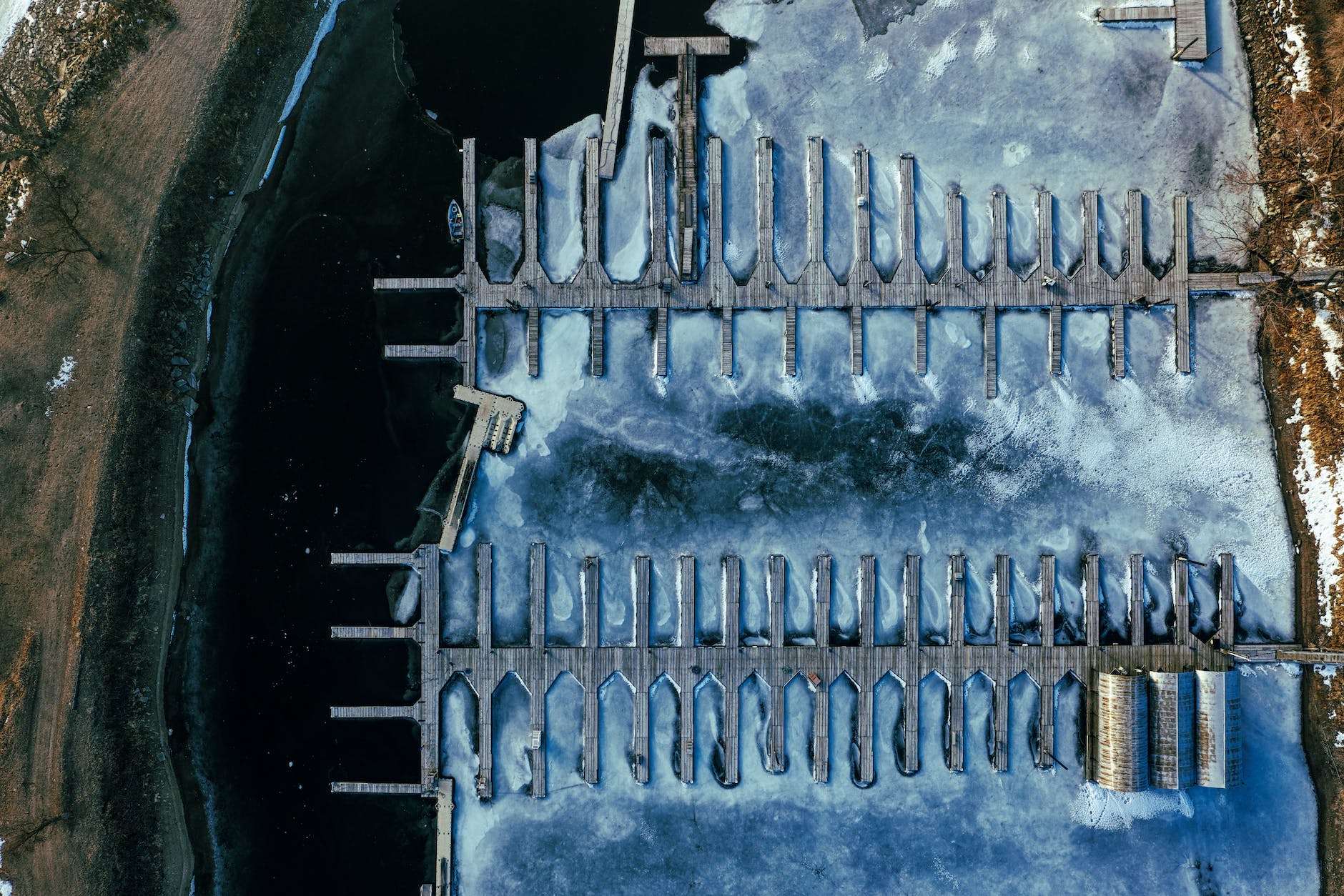
W dzisiejszych czasach automatyzacja procesów produkcyjnych odgrywa kluczową rolę w poprawie efektywności i konkurencyjności przedsiębiorstw. Jednakże, ocena stopnia automatyzacji może być trudnym zadaniem dla wielu firm. Istnieje wiele czynników, które należy wziąć pod uwagę przy analizie procesu produkcyjnego, takich jak rodzaj wykorzystywanych maszyn i technologii, poziom integracji systemów oraz wskaźniki wydajności. Warto zwrócić uwagę na te aspekty i dokładnie ocenić stopień automatyzacji swojej produkcji, aby osiągnąć maksymalne korzyści dla firmy.
Jak ocenić stopień automatyzacji procesu produkcyjnego – wprowadzenie do tematu
Automatyzacja procesów produkcyjnych jest nieodłącznym elementem współczesnej przemysłowości. Wprowadzenie nowoczesnych technologii i systemów automatycznych pozwala na zwiększenie efektywności, poprawę jakości produktów oraz redukcję kosztów produkcji. Jednak aby móc ocenić stopień automatyzacji w danym zakładzie, konieczne jest dokładne zrozumienie tego pojęcia.
Automatyzacja to wykorzystanie różnego rodzaju technologii i narzędzi do wykonania czynności lub procesu bez udziału człowieka. Może obejmować zarówno proste maszyny jak i zaawansowane systemy sterowania.
Ocena stopnia automatyzacji polega na analizie różnych aspektów produkcji, takich jak: ilość pracowników zaangażowanych w proces, liczba maszyn stosowanych w linii produkcyjnej, wykorzystywane technologie czy też wskaźniki efektywności. Daje to możliwość porównania aktualnego stanu z docelowym modelem automatyki.
Kluczowe wskaźniki efektywności – pomiar automatyzacji w produkcji
Aby dokonać rzetelnej oceny stopnia automatyzacji w danym zakładzie produkcyjnym, niezbędne jest zdefiniowanie kluczowych wskaźników efektywności. Są to miary, które pozwalają na monitorowanie i porównywanie wyników produkcji w czasie.
Jednym z najważniejszych wskaźników jest wskaźnik automatyzacji, który określa procentowy udział procesu produkcyjnego wykonywanego przez maszyny lub systemy automatyczne. Im wyższy wskaźnik, tym większy stopień automatyzacji.
Innym istotnym wskaźnikiem jest wydajność linii produkcyjnej, czyli ilość produktów wykonanych w jednostce czasu. Wysoka wydajność może świadczyć o dobrze zoptymalizowanym procesie produkcyjnym, gdzie wiele czynności zostało zautomatyzowanych.
Kolejny ważny aspekt to jakość produktu. Automatyzacja pozwala na precyzyjne kontrolowanie parametrów produkcji oraz eliminację błędów ludzkich. Dlatego wysoka jakość końcowych produktów może być sygnałem wysokiego stopnia automatyzacji.
Technologie automatyzacyjne – od prostych maszyn po zaawansowane systemy
Automatyzacja procesu produkcyjnego opiera się na różnych technologiach, począwszy od prostych maszyn aż do zaawansowanych systemów sterowania i robotyki.
Jednym z podstawowych narzędzi automatyzacji są maszyny, które wykonują powtarzalne czynności, takie jak obróbka, montaż czy pakowanie. Mogą być sterowane ręcznie lub za pomocą prostych programów.
Kolejnym krokiem w automatyzacji jest wykorzystanie systemów sterowania, które pozwalają na koordynację pracy różnych maszyn oraz monitorowanie procesu produkcyjnego. Zaawansowane systemy mogą być programowane do wykonywania skomplikowanych operacji i reagowania na zmienne warunki produkcji.
Robotyka to kolejny obszar technologii stosowany w celu automatyzacji procesów produkcyjnych. Roboty przemysłowe są zdolne do wykonywania wielu czynności, od prostych po bardzo skomplikowane, co znacznie zwiększa efektywność produkcji.
Integracja systemów – jak skutecznie połączyć różne elementy automatyzacji?
Aby zapewnić sprawną i efektywną pracę całego systemu automatycznego, niezbędna jest integracja poszczególnych jego elementów. Integracja polega na połączeniu różnych urządzeń i oprogramowania w jedną spójną całość.
Sterowniki PLC (Programmable Logic Controller) pełnią kluczową rolę w integracji systemów automatyzacyjnych. Są to specjalne urządzenia, które kontrolują pracę maszyn i oprogramowania oraz umożliwiają komunikację między nimi.
Ważnym aspektem integracji jest również wymiana danych pomiędzy poszczególnymi elementami systemu. Dane mogą być przesyłane za pomocą różnych protokołów komunikacyjnych, takich jak Ethernet czy Modbus.
Kolejnym krokiem w integracji jest zapewnienie jednolitego interfejsu użytkownika, który umożliwi łatwe sterowanie i monitorowanie całego procesu produkcyjnego. Dzięki temu operator może efektywnie zarządzać systemem automatycznym.
Szkolenie pracowników – rola ludzi w zautomatyzowanym środowisku produkcyjnym
Mimo postępującej automatyzacji, rola ludzi w procesach produkcyjnych nadal pozostaje istotna. Pracownicy pełnią kluczową rolę przy obsłudze i konserwacji maszyn oraz monitorowaniu pracy systemów automatycznych.
Aby zapewnić skuteczną współpracę między człowiekiem a technologią, niezbędne jest odpowiednie szkolenie pracowników. Pracownicy powinni posiadać odpowiednie umiejętności techniczne oraz zdolność do obsługi i programowania maszyn.
W zautomatyzowanym środowisku produkcyjnym ważne jest również bezpieczeństwo. Pracownicy powinni być odpowiednio przeszkoleni w zakresie bezpiecznej pracy przy maszynach oraz korzystania z systemów automatycznych.
Ponadto, szkolenia mogą pomóc pracownikom w lepszym zrozumieniu procesu produkcyjnego i identyfikacji potencjalnych problemów czy usterek. Dzięki temu mogą aktywnie wspierać działania mające na celu utrzymanie efektywnej automatyzacji.
Monitorowanie i diagnostyka – utrzymanie efektywnej automatyzacji
Aby zapewnić ciągłość pracy systemów automatycznych, konieczne jest ich regularne monitorowanie oraz diagnozowanie ewentualnych problemów. Monitorowanie pozwala na bieżąco kontrolować parametry produkcji oraz wykrywać awarie lub nieprawidłowości.
Czujniki są jednym ze sposobów monitorowania stanu urządzeń. Mogą mierzyć różne parametry, takie jak temperatura, wilgotność czy napięcie elektryczne. Dzięki nim można szybko reagować na zmiany warunków produkcji.
Kolejnym narzędziem jest diagnostyka, która polega na analizie danych i wykrywaniu potencjalnych problemów. Zaawansowane systemy diagnostyczne mogą przewidywać awarie oraz sugerować optymalizacje procesu produkcyjnego.
Ważnym aspektem monitorowania i diagnostyki jest raportowanie. System powinien generować raporty z wynikami produkcji, wskaźnikami efektywności oraz ewentualnymi usterek lub awariami. Dzięki temu można podejmować odpowiednie działania naprawcze.
Perspektywy rozwoju – jak planować rozbudowę automatyzacji w przemyśle?
Rozwój technologii automatyzacyjnych otwiera nowe możliwości dla przemysłu. Planowanie rozbudowy automatyzacji wymaga jednak strategicznego podejścia i uwzględnienia różnych czynników.
Analiza potrzeb to pierwszy krok w planowaniu rozbudowy. Należy dokładnie określić, które obszary produkcji wymagają większej automatyzacji oraz jakie cele chce się osiągnąć poprzez wprowadzenie nowych technologii.
Kolejnym etapem jest wybór odpowiednich rozwiązań. Na rynku dostępne są różne technologie i systemy, dlatego ważne jest dokładne zrozumienie ich funkcjonalności oraz korzyści jakie mogą przynieść dla danego zakładu produkcyjnego.
Ważnym aspektem jest również planowanie inwestycji. Automatyzacja procesów produkcyjnych może wymagać znacznych nakładów finansowych, dlatego ważne jest dokładne oszacowanie kosztów oraz analiza zwrotu z inwestycji.
Ostatecznie, kluczowym elementem planowania rozbudowy automatyzacji jest wdrożenie. Proces ten powinien być przeprowadzony w sposób stopniowy i uwzględniać szkolenie pracowników oraz dostosowanie infrastruktury do nowych technologii.